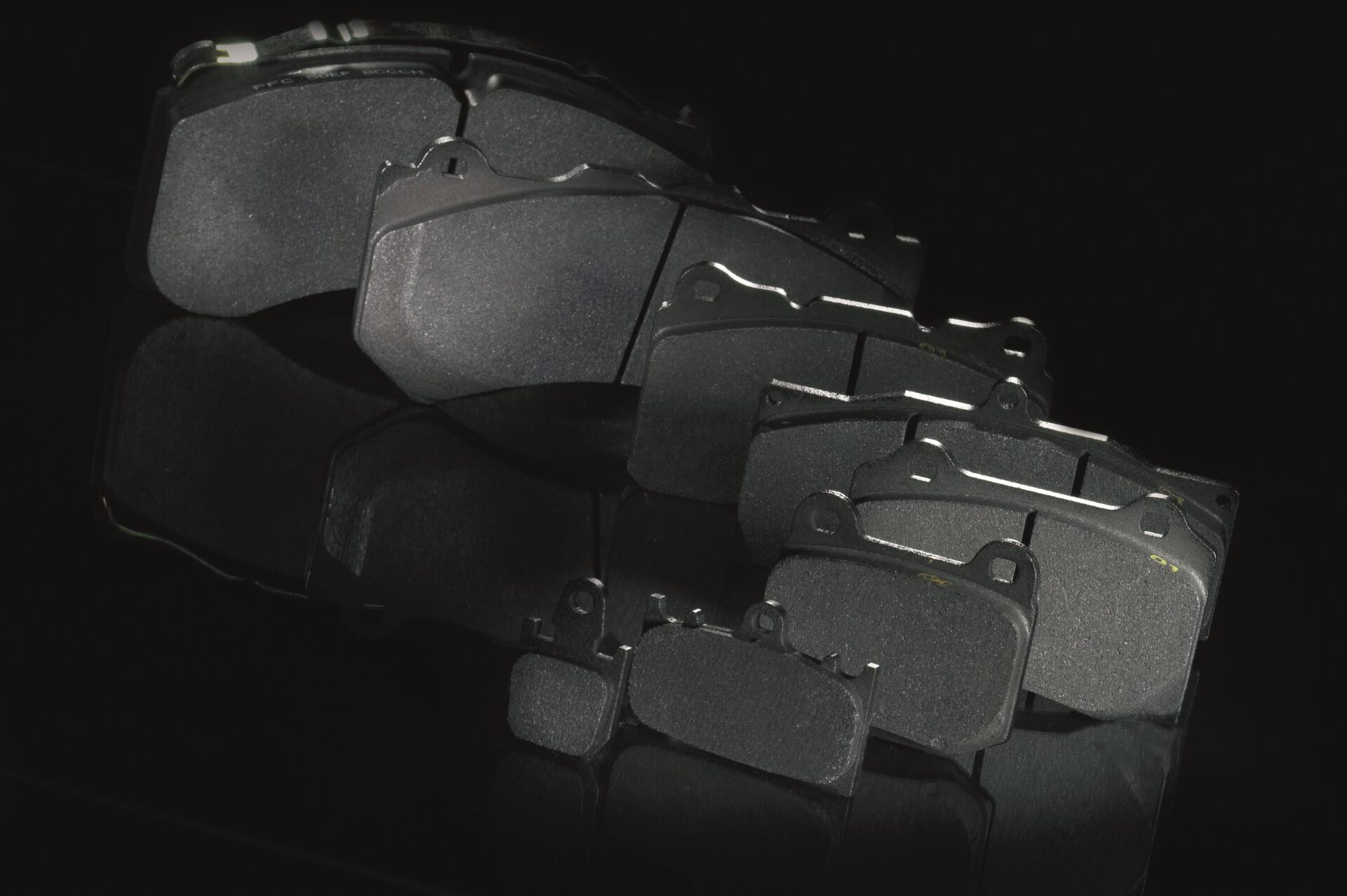
Bedding Procedures
Proper Bedding Procedure For Your Carbonmetallic® Raceready® Pads
If the discs were previously being used with PFC brake pads then the bedding-in procedure will be achieved quickly with new PFC pads. Discs previously bedded using a different manufacturer’s pads require a slightly longer process. With brake cooling ducts open and fully functional, perform the following procedures.
All PFC RaceReady® brake pads are pre-treated to be race and street ready. This treatment is done in the final step of the manufacturing process when the surface of the friction material is brought up to temperature in order to simulate a bedding cycle. However, proper bedding is still required using your rotors with the new CarbonMetallic® pads. The following process below is suggested in order to achieve the best performance, consistency and durability of the brake pad.
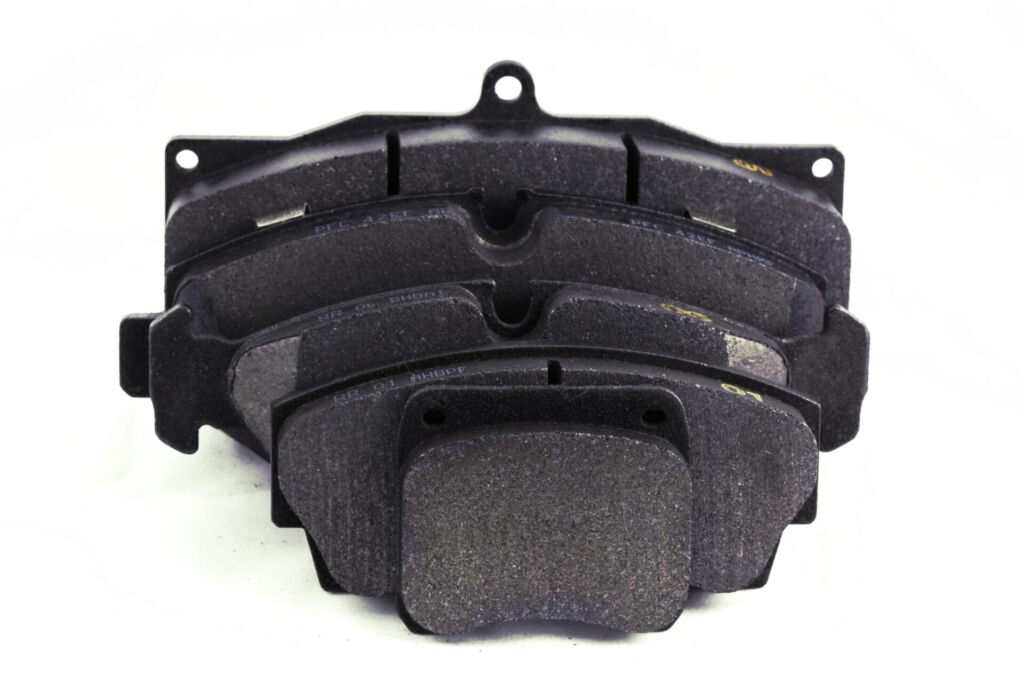
Step 1
On the first lap, perform several stops with progressively higher pedal pressure and braking force and from higher speeds. You will feel the effectiveness of the brakes increase with each successive brake application.
Step 2
This should take six to ten snubs per lap and is usually completed in one or two laps. If non-PFC friction materials were previously run on the discs then this procedure could take as many as three to five laps.
Step 3
Running additional laps is the best way to accomplish the new transfer layer and, due to the higher surface temperatures, will ensure the complete removal of the old friction materials from the disc.
Step 4
The disc should be allowed to cool as much as is practical, with ambient temperature being ideal. Allowing the disc to cool to ambient temperature will increase disc life and performance.
Step 5
The pads are now properly bedded to provide consistent performance. The pads should be brought back up to the operating temperature range to guarantee optimum braking power. This depends upon the specific compound.
Aftermarket Brake Pad Bedding Procedure
All PFC brake pads are pre-treated to be race and street-ready. This treatment is done in the final step of the manufacturing process when the surface of the friction material is brought up to temperature in order to simulate a bedding cycle. However, proper bedding is still required using your discs with the new CarbonMetallic® & Z-rated brake pads.
The following process is suggested in order to achieve the best performance, consistency, and durability of the pad.
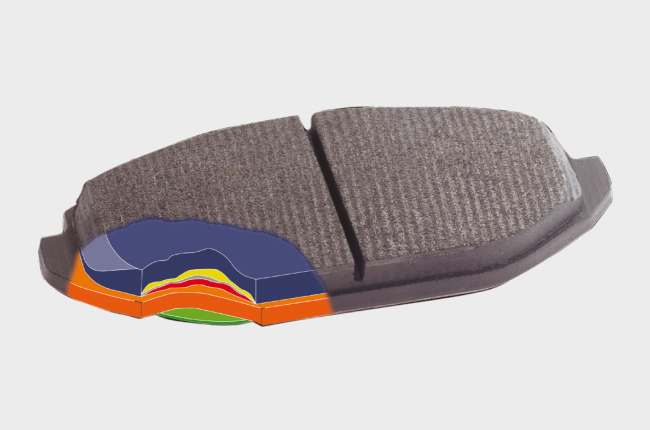
Step 1
Gradually get the PFC pads up to temperature. Do not spend a longer time on the brakes than usual because this can create thermal shock within the compound.
Step 2
Perform several stops with progressively higher pedal pressure and braking force and from higher speeds. You will feel the effectiveness of the brakes increase with each successive brake application.
Step 3
Continuing this procedure a few more times is the best way to accomplish the new transfer layer and, due to the higher surface temperatures, will ensure the complete removal of the old friction materials from the disc.
Step 4
The disc should be allowed to cool as much as is practicable, with ambient temperature being ideal. Disc life and performance will be increased if allowed to cool to ambient temperature.
Step 5
The discs are now properly bedded to provide consistent performance. The pads should be brought back up to the operating temperature range to guarantee optimum braking power. This depends on the specific pad compound.
Motorcycle Race Brake Pad Bedding-In Procedure
All PFC motorcycle brake pads are pre-treated to be race-ready. This treatment is done in the final step of the manufacturing process when the surface of the friction material is brought up to temperature in order to simulate a bedding-in cycle. However, a proper bed-in process is still required using your discs with new Carbon Metallic pads.
The following process below is suggested in order to achieve the best performance, consistency, and durability of the pad.
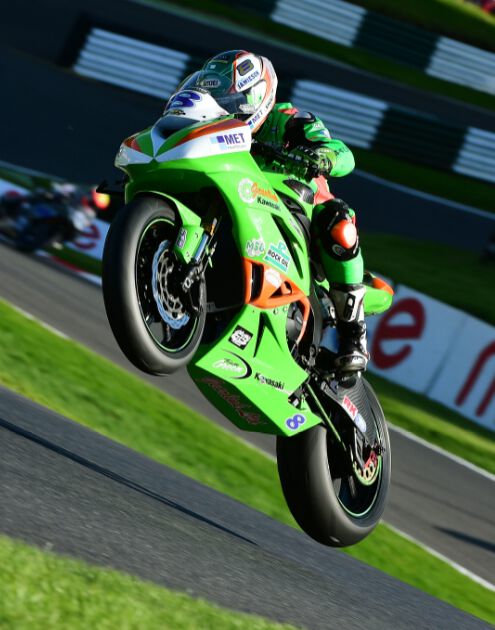
Step 1
Remove the residual pad material from the disc surface to prevent judder on the lever and inconsistent brake torque. This is especially important if the previous pad was a sintered compound. Light-duty Scotch Brite (3M 07448) or Flex-Hone can be used for this purpose.
Step 2
Gradually get the PFC pads up to temperature for approximately three to four laps. Make the first lap at half pace using the brake as normal. Do not spend a longer time on the brakes than usual as this can create a thermal shock within the compound.
Step 3
Complete two more laps, gradually increasing the pace and pressure on the brakes. The last lap should be at a normal pace.
Step 4
After running for three to four laps enter the pits and apply the brakes hard twice. This helps to create a uniform layer of brake pad material on the disc surface. As a result, it improves the modulation of the brake application.
Step 5
Cool the brakes off at ambient temperature, so that the heat transfer from the disc and pads is slow and gradual. This helps to increase the duration of the pad, as well as the smoothness of the application.
Step 6
The pads are now properly bedded to provide consistent performance. They should be brought back up to the operating temperature range to guarantee optimum braking power. This depends upon the specific compounds.
Find Parts and Distributors
Looking for PFC Brake parts or a distributor near you? Use our parts finder to look up specific parts or our distributor locator map to find a local distributor in your area.
connect with a PFC Product Specialist
Our team is standing by and ready to help you find the right parts, discuss performance, or answer general questions.